Introduction to Busbar Trunking Systems
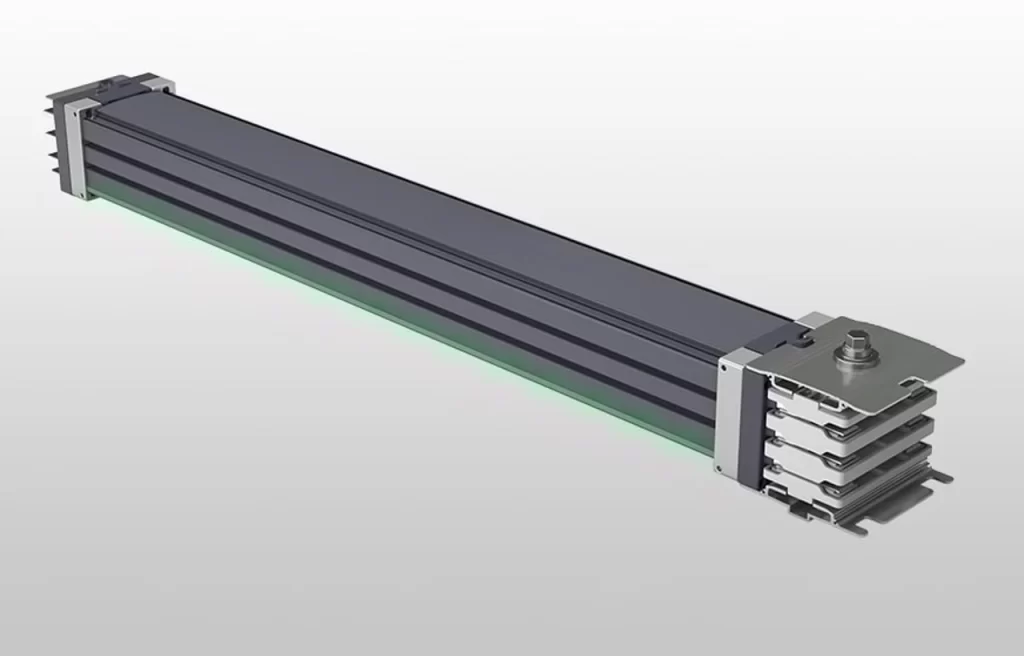
Busbar trunking systems, also known as busbar trunking systems, represent a modern approach to electrical power distribution within buildings and industrial facilities. These systems offer a highly efficient and versatile solution for transmitting electricity from the main power supply to various distribution points. Busbar trunking comprises a series of copper or aluminum bars housed within an enclosure, providing a safe and reliable method for power transmission.
One notable feature of busbar trunking systems is their flexibility in design and installation. Unlike traditional wiring methods, which involve extensive cable laying, busbar trunking utilizes pre-fabricated components that can be easily configured to suit specific layout requirements. This streamlined installation process not only reduces labor costs but also minimizes downtime during construction or upgrades.
Moreover, overhead bars in buses contribute to the space-saving nature of these systems, as they can be installed overhead or along walls, freeing up valuable floor space. This makes busbar trunking systems particularly advantageous in environments where space is limited, such as high-rise buildings or manufacturing plants.
In summary, busbar trunking systems offer a robust and efficient solution for electrical power distribution, characterized by their flexibility, reliability, and space-saving design.
Benefits of Busbar Trunking Systems
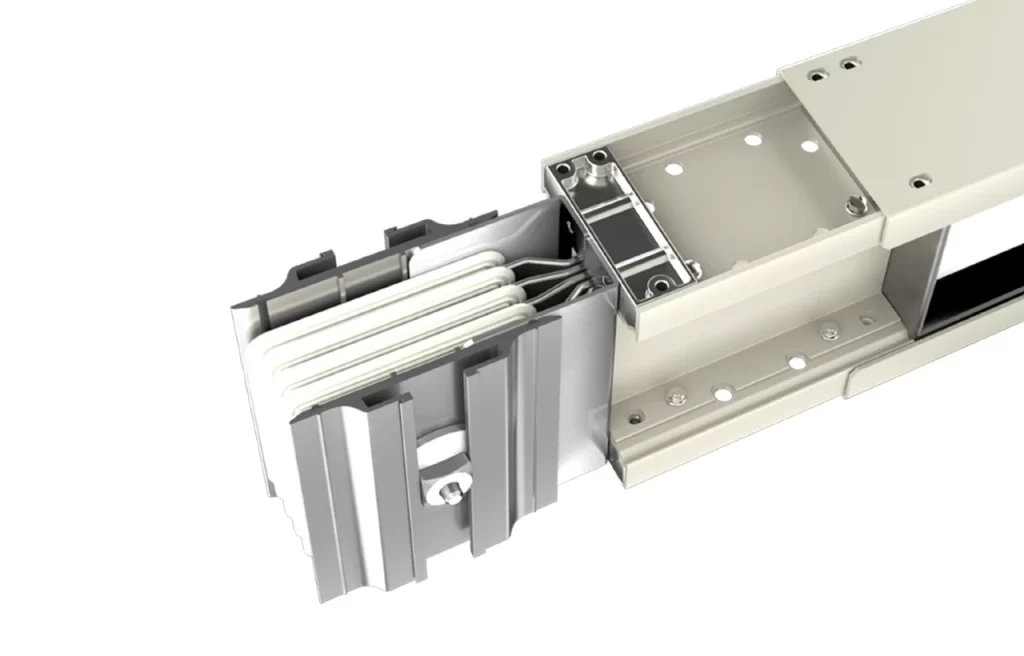
Busbar trunking systems offer several efficiency and functionality advantages compared to traditional wiring methods. Here are the key benefits:
Enhanced Efficiency: Busbar trunking systems provide a streamlined approach to electrical power distribution, reducing energy losses associated with traditional wiring methods.
Flexibility in Design: With busbar trunking systems, overhead bars in bus can be easily configured to adapt to various building layouts and requirements, allowing for efficient utilization of space and resources.
Increased Reliability: The design of busbar trunking systems ensures consistent and reliable power transmission, minimizing the risk of electrical faults and downtime.
Cost-effectiveness: Despite initial installation costs, busbar trunking systems offer long-term savings due to their durability, low maintenance requirements, and reduced need for costly cable replacements.
Safety: The enclosed design of busbar trunking systems enhances safety by minimizing the risk of electrical hazards, such as short circuits and fires, compared to exposed wiring systems.
Overall, busbar trunking systems provide a more efficient, reliable, and cost-effective solution for electrical power distribution, making them increasingly preferred over traditional wiring methods in various industrial and commercial applications.
Components and Design
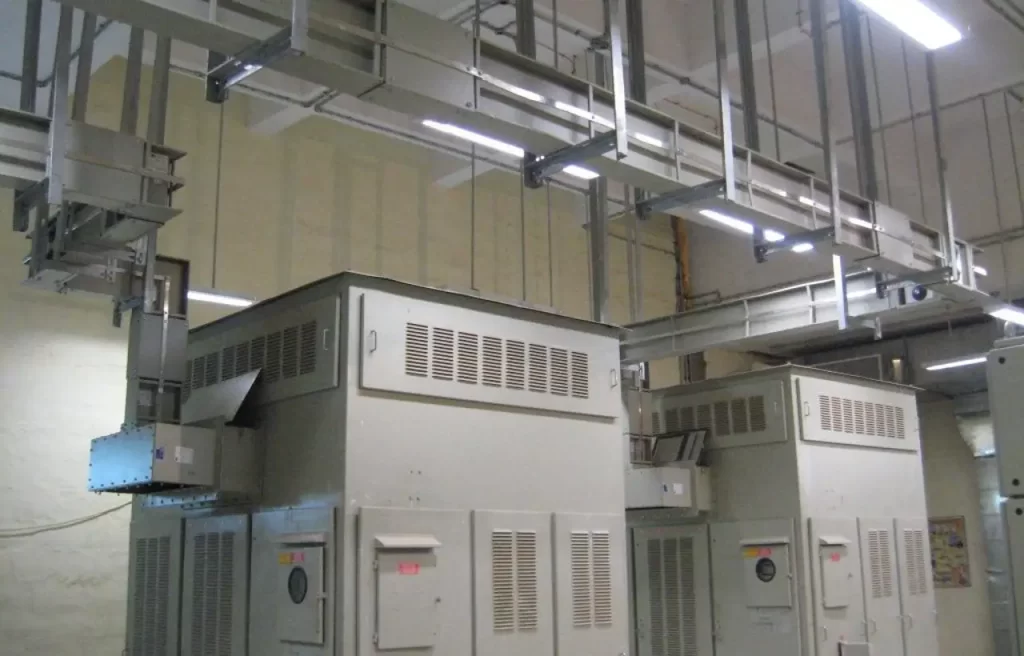
A busbar trunking system consists of several essential components meticulously designed to ensure optimal performance and efficiency in electrical power distribution. Here’s a breakdown of these components:
Busbars: The primary conductors of the system, busbars are typically made of copper or aluminum and carry the electrical current from the power source to the distribution points. These bars are enclosed within a protective housing to ensure safety and reliability.
Enclosures: Enclosures provide protection to the busbar trunking components against external elements and mechanical damage. They are designed to withstand environmental conditions and ensure the safety of the system.
Fittings and Accessories: These include various components such as joints, bends, tees, and reducers, which allow for the customization and flexibility of the busbar trunking system’s layout to suit specific installation requirements .
Overhead Bars in Bus: These bars are crucial elements of the system, providing support and stability to the busbar trunking components, especially in overhead installations. They ensure proper alignment and secure positioning of the system, enhancing its overall performance.
By meticulously integrating these components into the design, busbar trunking systems achieve optimal performance, reliability, and safety in electrical power distribution, making them indispensable in various industrial and commercial applications.
Installation Process
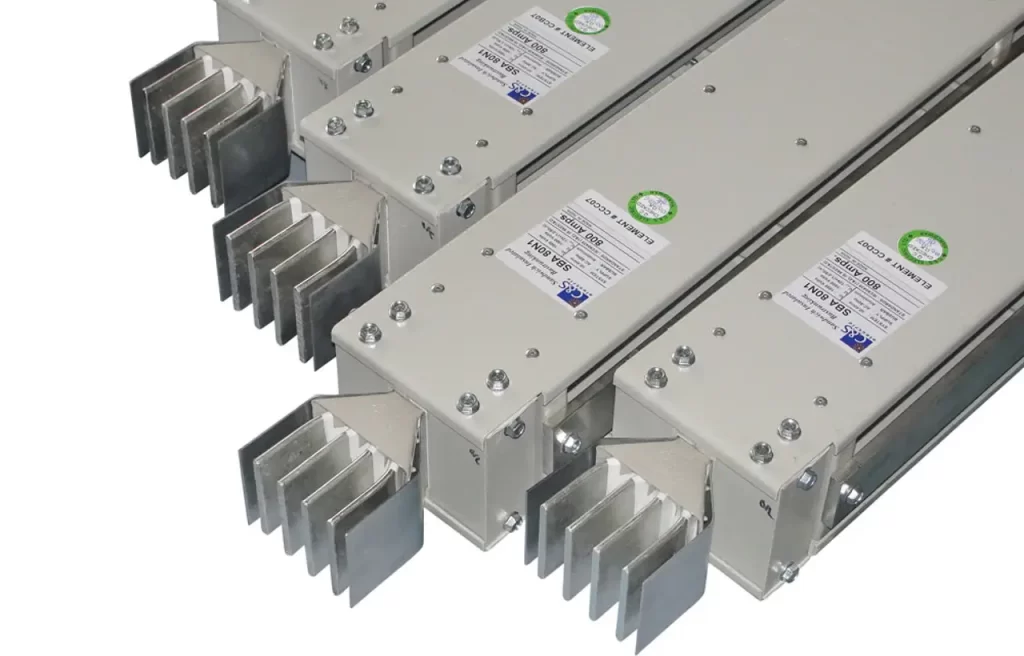
The process of a busbar trunking system installation is renowned for its simplicity and cost-effectiveness, making it a preferred choice for electrical power distribution in various settings. Here’s an overview of the installation procedure:
Preparation: Before installation, meticulous planning is essential to determine the layout and configuration of the busbar trunking system. This includes assessing the power distribution requirements, identifying suitable locations for mounting the system, and considering any specific needs such as overhead or wall-mounted installations.
Mounting: The busbar trunking components, including the busbars, enclosures, and fittings, are mounted according to the pre-determined layout. The flexibility of the system allows for easy adjustment and customization to accommodate diverse installation environments.
Connection: Once mounted, the busbars are connected to the power source and distribution points using secure fittings and connectors. This ensures a reliable electrical connection throughout the system.
Testing and Commissioning: After installation, thorough testing and commissioning are conducted to verify the integrity and functionality of the busbar trunking system. This includes checks for proper electrical conductivity, insulation, and safety features.
By following these steps, the installation of a busbar trunking system is completed efficiently and cost-effectively, providing a reliable and scalable solution for electrical power distribution needs.
Applications
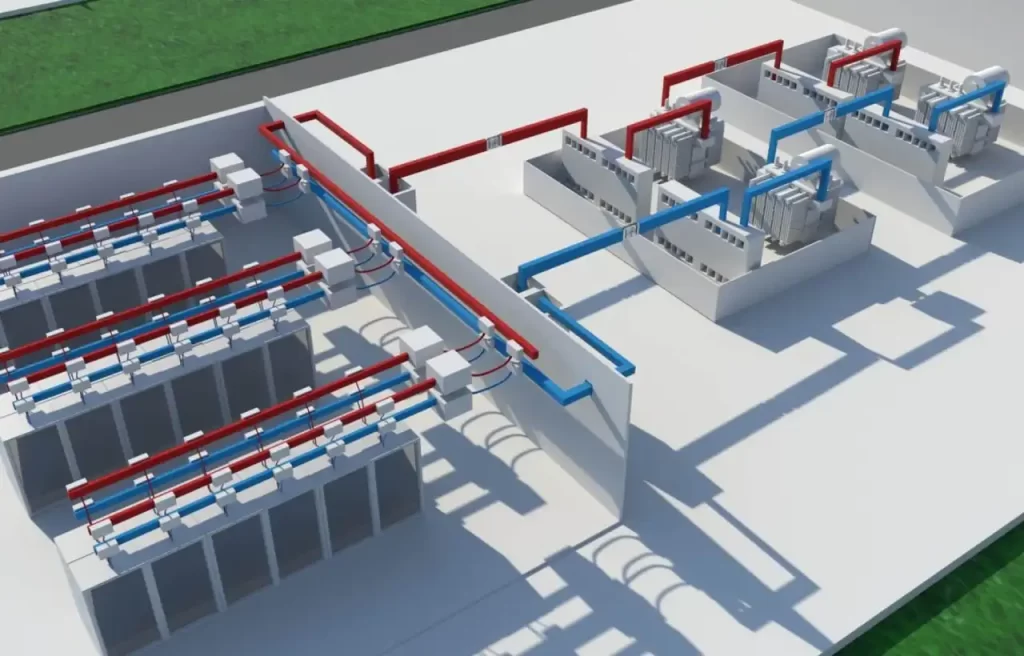
Busbar trunking systems find versatile applications across multiple industries due to their efficiency, reliability, and flexibility. Here are some key areas where these systems are commonly employed:
Commercial Buildings: In office complexes, malls, and commercial centers, busbar trunking systems efficiently distribute power to lighting, air conditioning, and other electrical loads. Their modular design allows for easy adaptation to evolving building layouts and requirements.
Industrial Facilities: Industries rely on busbar trunking for powering heavy machinery, conveyor belts, and manufacturing equipment. The robust construction of these systems ensures uninterrupted power supply even in demanding industrial environments.
Data Centers: With the increasing demand for data processing and storage, busbar trunking systems provide a reliable solution for distributing power to servers, networking equipment, and cooling systems. Their high power density and scalability make them ideal for data center applications.
Renewable Energy Integration: Busbar trunking plays a vital role in renewable energy installations such as solar and wind farms. These systems efficiently transmit power generated from renewable sources to the grid or local distribution networks.
Transportation: In transportation infrastructure like airports, railways, and metro systems, busbar trunking systems provide reliable power distribution for lighting, escalators, and signaling systems. Their compact design and ease of installation make them suitable for overhead installations in such environments.
By catering to diverse applications across various industries, busbar trunking systems demonstrate their versatility and effectiveness in meeting the evolving electrical power distribution needs of modern infrastructure.
Maintenance and Safety
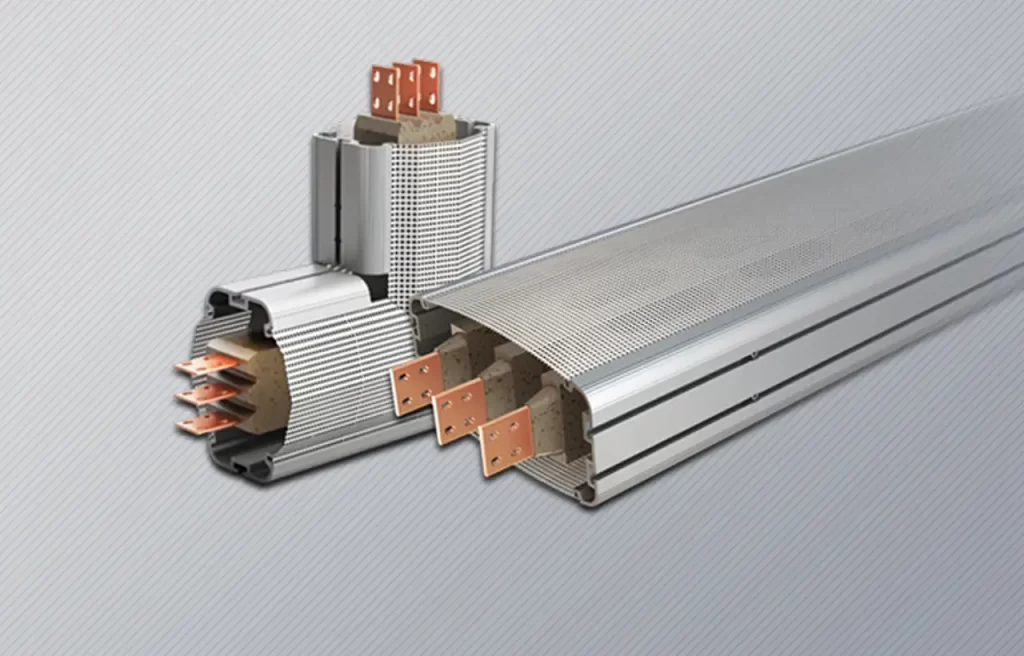
Regular maintenance and adherence to safety protocols are paramount in ensuring the reliable operation and longevity of busbar trunking systems. Here’s why:
Prevention of Failures: Routine maintenance helps identify potential issues such as loose connections, corrosion, or insulation degradation in busbar trunking systems. Addressing these issues promptly prevents failures that could lead to costly downtime and disruptions in power supply.
Safety Assurance: Proper maintenance practices mitigate safety hazards associated with busbar trunking, such as electrical shocks and fires. Inspections ensure that components are securely mounted, and insulation remains intact, reducing the risk of accidents.
Compliance with Regulations: Following maintenance, guidelines helps organizations comply with industry standards and regulations governing electrical installations. This ensures that busbar trunking systems meet safety requirements and operate within specified parameters.
Comparison with Alternative Systems
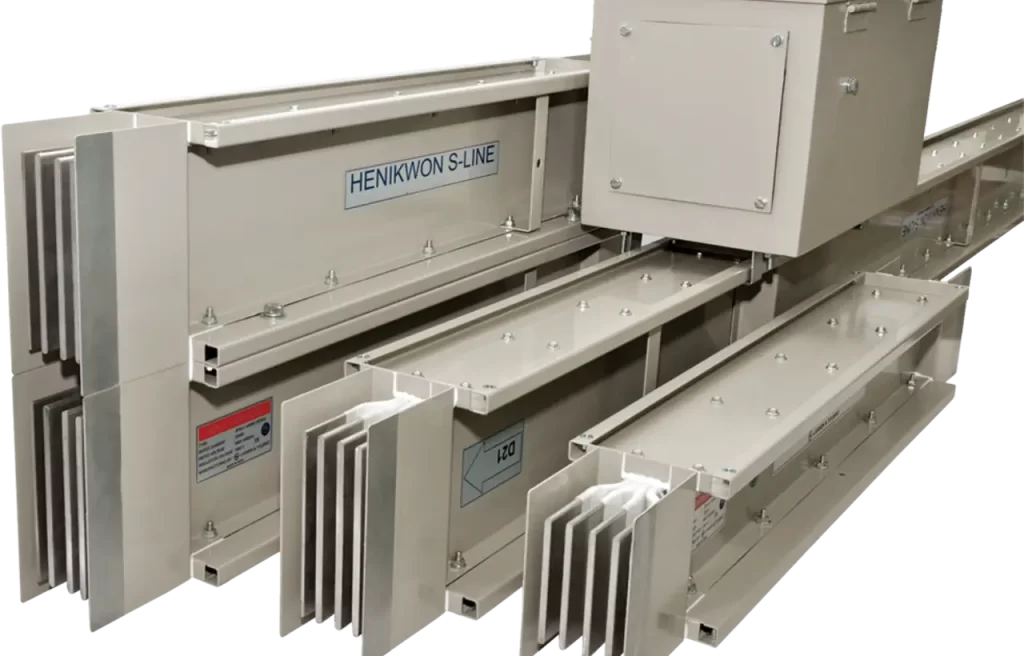
Busbar trunking systems offer several advantages over traditional electrical distribution methods, such as cable systems:
Efficiency: Unlike cables, which can suffer from voltage drops over long distances, busbar trunking maintains consistent power distribution with minimal energy loss. The conductors in busbar trunking are typically made of copper or aluminum, providing superior conductivity and efficiency.
Flexibility: Busbar trunking allows for easy modification and expansion of electrical networks. Additional tap-off points can be installed along the system without extensive rewiring, providing greater flexibility in adapting to evolving power demands.
Space Savings: Compared to bulky cable trays or conduits, busbar trunking systems have a compact design, saving valuable space in buildings and industrial facilities. This streamlined construction also reduces installation time and labor costs.
Safety: With their enclosed design, busbar trunking systems offer enhanced protection against electrical faults, such as short circuits and arc flashes. The insulated enclosures minimize the risk of accidental contact with live components, improving overall safety.
Overall, the efficiency, flexibility, space-saving design, and safety features of busbar trunking systems make them a superior choice for modern electrical distribution needs compared to conventional cable systems.
Long-Term Cost Savings: Proactive maintenance practices prolong the lifespan of busbar trunking systems and reduce the likelihood of costly repairs or replacements. They are investing in regular maintenance yields significant cost savings over time.
By prioritizing regular maintenance and safety measures, organizations can ensure their busbar trunking systems’ reliability, safety, and efficiency while minimizing operational risks and maximizing cost-effectiveness.
Future Trends
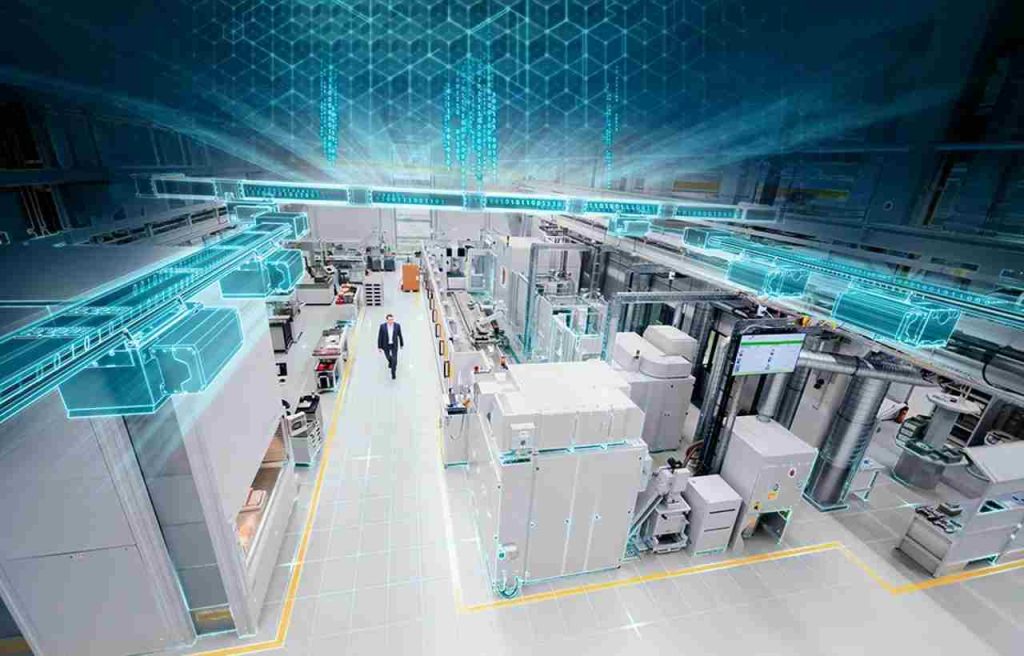
The future of busbar trunking systems is promising, with several emerging trends and advancements shaping their trajectory:
Smart Integration: Future busbar trunking systems are expected to incorporate smart technologies for enhanced monitoring, control, and efficiency. This integration will enable real-time data analytics, predictive maintenance, and energy optimization, making busbar trunking more adaptive to dynamic power demands.
Modular Design: Manufacturers are increasingly focusing on developing modular busbar trunking systems that offer scalability and flexibility. Modular designs allow for easier installation, expansion, and customization according to specific project requirements, catering to diverse applications across various industries.
Energy Efficiency: With a growing emphasis on sustainability, future busbar trunking systems will prioritize energy efficiency and eco-friendliness. Integration of advanced materials and technologies, such as energy-efficient conductors and insulation materials, will reduce power losses and environmental impact, aligning with global energy conservation goals.
Increased Market Penetration: The busbar trunking system market is projected to witness substantial growth, driven by rapid urbanization, industrialization, and infrastructure development. As demand for reliable and cost-effective power distribution solutions rises, busbar trunking is expected to penetrate new sectors and regions, further expanding its market presence.
These trends underscore the potential of busbar trunking systems to revolutionize electrical distribution, offering efficiency, flexibility, and sustainability for diverse applications in the future.
FAQs
What are the two types of busbar trunking?
- The two main types of busbar trunking are sandwich type and air-insulated type.
- Sandwich Type: Consists of conductors sandwiched between layers of insulation, providing high safety and reliability.
- Air-insulated Type: Utilizes air as the insulating medium between conductors, offering cost-effectiveness and flexibility.
Why is busbar trunking used in factories?
- Busbar trunking is preferred in factories due to its efficiency in electrical power distribution.
- Enhanced Efficiency: Provides a compact and efficient method of distributing electricity, reducing installation time and costs.
- Flexibility: Offers flexibility in layout and capacity adjustments to accommodate changing factory setups.
What is the advantage of busbar trunking?
- The primary advantage of busbar trunking is its efficiency and versatility in power distribution.
- Cost-effectiveness: Reduces installation and maintenance costs compared to conventional cable systems.
- Space-saving: Occupies less space and allows for easier expansion or modification of electrical installations.
What is an overhead busbar trunking system?
- An overhead busbar trunking system is a type of busbar trunking that is installed overhead, typically on ceilings or structural supports.
- Space Optimization: Ideal for environments where floor space is limited or where underground installation is impractical.
- Accessibility: Allows for easy access for maintenance and modifications without disrupting operations.